Absolutely, you can use iron-on vinyl (also known as heat transfer vinyl or HTV) on picture frame mats! This is a fantastic way to personalize and add a unique touch to your framed photos or artwork. Here are some steps to guide you through the process:
Materials Needed:
- Picture frame mat
- Iron-on vinyl (HTV)
- Cutting machine (like a Cricut or Silhouette) or scissors
- Weeding tool
- Iron or heat press
- Parchment paper or Teflon sheet
Steps:
- Design Your Vinyl Cut:
- Create or choose a design that you want to apply to the mat. You can use design software compatible with your cutting machine or even Creative Fabrica Studio for some fantastic templates and design elements.
- Cut the Vinyl:
- Load your iron-on vinyl into your cutting machine, making sure to mirror your design if it includes text. Cut out your design.
- Weed the Vinyl:
- Use a weeding tool to remove the excess vinyl, leaving only your design on the carrier sheet.
- Prepare the Mat:
- Place the picture frame mat on a flat, heat-resistant surface. Make sure it's clean and free of dust.
- Position the Vinyl:
- Place your weeded design onto the mat, with the carrier sheet facing up. Ensure it's positioned exactly where you want it.
- Apply Heat:
- Cover the vinyl with parchment paper or a Teflon sheet to protect it. Use an iron or heat press to apply heat and pressure to the vinyl. If using an iron, set it to the cotton setting (no steam) and press down firmly for about 10-15 seconds. If using a heat press, follow the manufacturer's instructions for HTV.
- Peel the Carrier Sheet:
- Allow the vinyl to cool slightly, then carefully peel off the carrier sheet. If the vinyl is not fully adhered, reapply heat as needed.
- Assemble the Frame:
- Once the vinyl is securely adhered to the mat, place the mat back into the frame with your photo or artwork.
And voilà! You now have a beautifully customized picture frame mat. This technique can add a personal touch to gifts, home decor, or even special event displays. Happy crafting! 🌟
More Related Questions
Applying rhinestones can be a delightful way to add some sparkle to your projects, whether you're decorating clothing, accessories, or home decor.
Permanent Rhinestone Adhesives
E6000
A popular choice for crafters, E6000 is a strong adhesive that dries clear and provides a durable hold. It's perfect for attaching rhinestones to various surfaces such as fabric, metal, glass, and more.
Gem-Tac
This is another well-known glue for rhinestones, especially on fabric. It dries clear, is flexible once cured, and is washable, making it ideal for clothing and fabric projects.
Hypo Cement
Preferred for fine detail work, Hypo Cement is great for small projects or intricate designs. It's precise and dries clear, though it may not be as strong as E6000 or Gem-Tac for heavier use.
Tips for Using Rhinestone Glue
Surface Preparation
Ensure that the surface is clean and dry before applying glue to ensure the best adhesion.
Application Technique
Use a toothpick or a fine-tip applicator to place a small amount of glue directly where the rhinestone will sit, avoiding excess to keep the project clean.
Curing Time
Allow ample time for the glue to cure fully. This could range from 24 to 72 hours, depending on the adhesive used, before the item can be handled or washed.
With the right adhesive, your rhinestone projects will shine brightly and stay securely in place. Happy crafting! ✨
How come my marker is dragging across my paper when it moves from letter to letter?
Im looking for button pin designs that are for kids between the ages of 5 and 12. It must be fun, funky and creative designs?
Does anyone know how to make a tote bag that is made with one long piece of cloth then folded halfway for the bottom and stitched up the sides ( it is lined after but for the outer part it's one single piece of fabric?
Can I sell a coloring book on Etsy and Amazon using creative fabrica images? If I alter them, how much do I have to alter them?
I downloaded the "lucky feelings" font, It doesn't have the same look as the it shows. How can I fix this? I have a project already done and I need to redo some of the lettering, but can't get it the way it was.
Can you help me find a font that I KNOW is on CreativeFabrica?
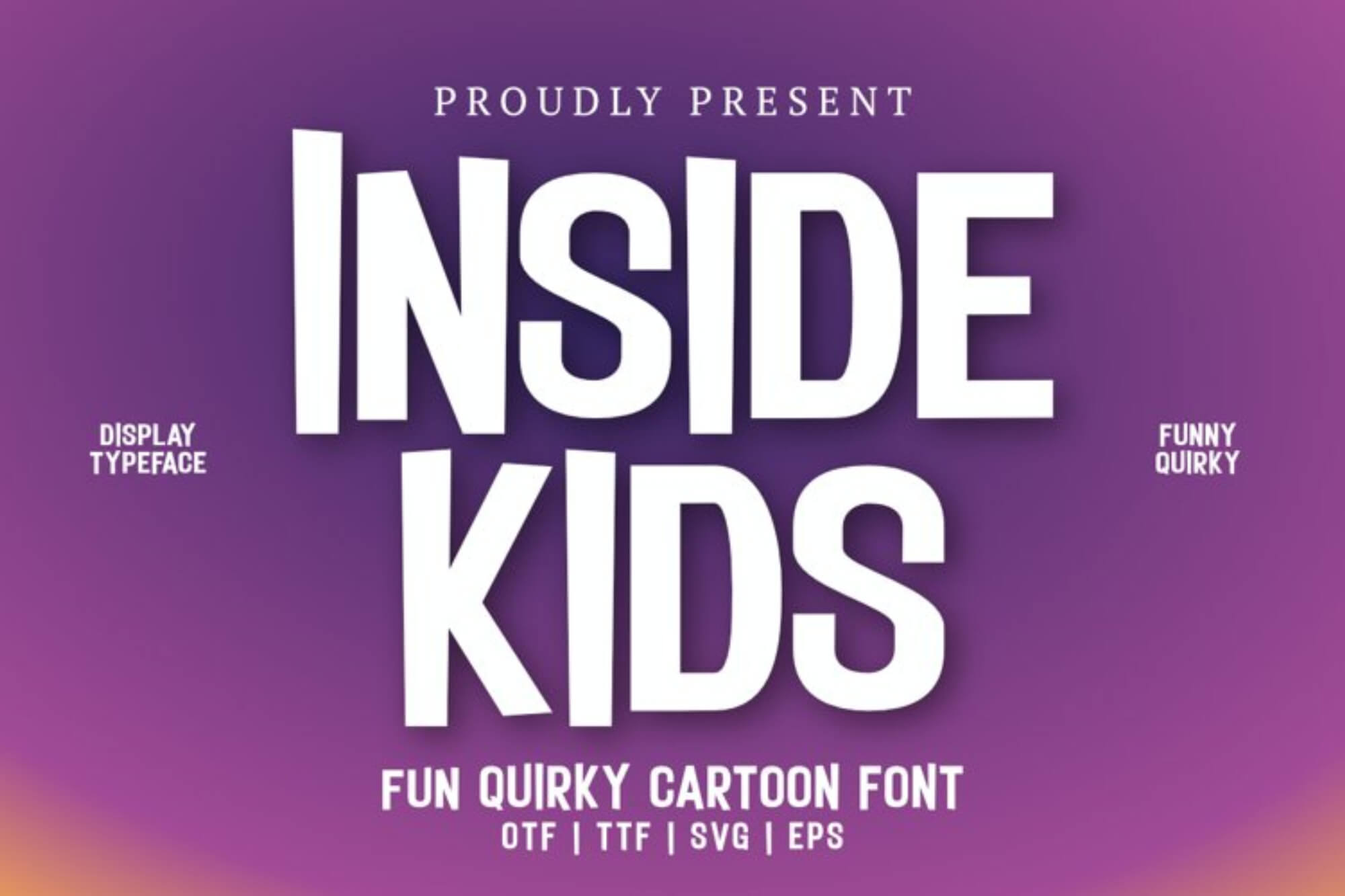