Hi I'm trying to make a belly wraps for my trinket trays using my own logo. I've tried using rectangle shape and putting logo in the middle but I'm stuck. I want it to be print and cut. Help please?
Creating a belly wrap for your trinket trays with your own logo is a delightful way to personalize your products! Here's a step-by-step guide to help you out.
Designing the Belly Wrap
Step 1: Choose Dimensions
Determine the width and height of the belly wrap. Ensure it's long enough to wrap around the tray with some overlap for fastening.
Step 2: Use Design Software
Utilize design software like Adobe Illustrator, CorelDRAW, or Creative Fabrica's Studio to create your design.
Step 3: Incorporate Your Logo
Place your logo centrally on the design. Consider scaling the logo to fit proportionately within the constraints of your wrapβs design.
Step 4: Add Decorative Elements
Add any additional elements such as borders, patterns, or colors to complement your logo while maintaining overall harmony.
Step 5: Check Printing Margins
Ensure there's enough margin around the edges to avoid cutting off any important parts of the design during the printing process.
Preparing for Print and Cut
Step 1: Use Cutting Software
Import your design into a print and cut software like Cricut Design Space or Silhouette Studio.
Step 2: Set Cut Lines
Designate where the machine should cut. Ensure thereβs a border around your design, if needed.
Step 3: Print the Design
Use a printer with good color accuracy to print your design onto adhesive paper or standard paper.
Step 4: Align for Cutting
Place the printed sheet on your cutting mat and align it in your cutting machine. Follow the software's instructions for precise cutting.
And there you have it! A beautifully personalized belly wrap for your trinket trays. Enjoy wrapping them up and showcasing your unique style!
More Related Questions
Magic Seal products can be useful for sealing your heat transfer vinyl (HTV) and sublimation projects to help protect the design and enhance durability.
Key Benefits of Using Magic Seal
Protects the Design
By sealing the surface, you can protect the design from wear and tear, which is particularly beneficial for items that will be washed or used frequently.
Enhances Color Vibrancy
Sealers can enhance the vibrancy of colors on printed designs, making them stand out more beautifully.
Considerations for Using Sealants
Ensure that your sealant is compatible with the specific materials you're using. Test it on a small area first to avoid any unwanted reactions.
While specific experiences with Magic Seal can vary, many crafters find sealants helpful in preserving their projects. It's always exciting to see how different crafters achieve their desired results!
What product works best for coloring etched glass? I have acrylic markers but they don't fill in large areas well. The larger areas become streaky.
Coloring etched glass can be a magical way to add a pop of color and vibrancy to your finished project.
Best Products for Coloring Etched Glass
Glass Paints
Using glass paints is an excellent option for coloring etched glass. They are specifically formulated to adhere to glass surfaces and provide a smooth, vibrant finish. Brands like Pebeo and Vitrea 160 offer paints that can be air-dried or baked for increased durability.
Alcohol Inks
Alcohol inks are another wonderful choice, as they provide rich, fluid colors that spread evenly. Applying them with a felt pad or a brush can help in achieving even coverage, even on larger areas.
Oil-Based Paint Pens
Unlike acrylic pens, oil-based paint pens offer a more consistent finish on glass surfaces. They are designed to be permanent and have better opacity, reducing streakiness for larger areas.
Experimenting with these options can help you achieve the perfect look for your etched glass projects. Remember to always test on a small area first. Happy crafting! π¨β¨
What recommendations can be made for choosing the best mediums and specific created art types, that need to be placed in a collection that's curated specifically for CF store applications?
For a retail display window that will be exposed to UV rays, is it best to use vinyl applied directly to the window or use a stencil and then apply paint? For either route, what type of material is best?
Can you sublimate something flat like a coated glass cutting board in a sublimation oven instead of using a heat press or do you need the pressure from the press in addition to the heat?
What is the BEST printer for Print and Cut projects? THANKS for any help "-)?
Iβd like to try sublimating glass cutting boards/frames but found the white backing of the sublimation blank washes out the color. Is there an alternative?
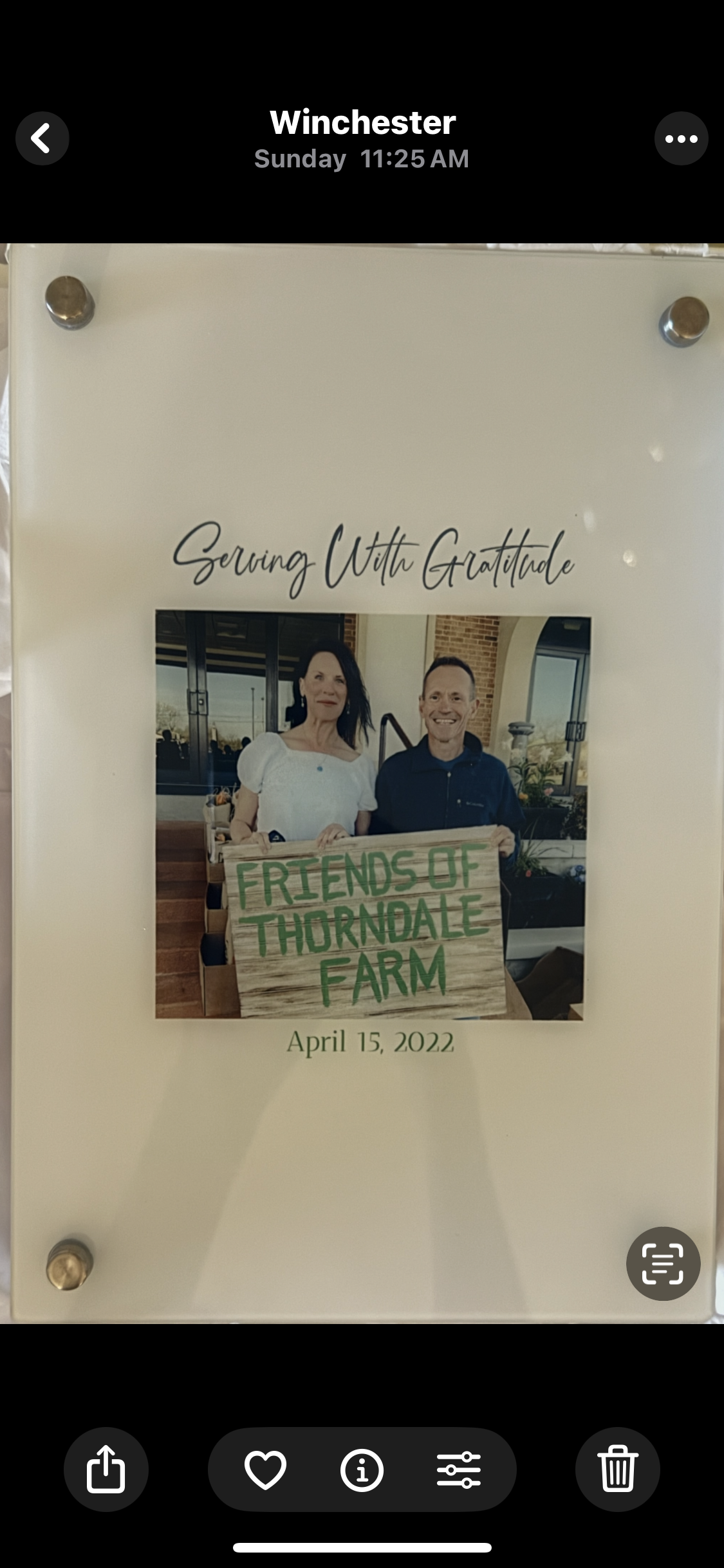